Saturday, September 15, 2007
The Grill - Technical Drawing
Here is my technical drawing. It's more or less final, but I'm still working on a few design issues. I want the side table to fold out, so the grill is more compact when stored. It should also be sturdy and without wobble when it is extended. It's hard to get both. I've settled on a system with a free hinge and two support rods that lock into the table when it is out, sort of like the rod that holds up a car hood. It will work, but I'd like a more elegant solution. Bob Woods, my instructor, suggested that there are prefab hinged arms to do just this task. Fortunately, the table will be one of the last parts I build, so I have plenty of time to figure this one out.
Beginning the Grate



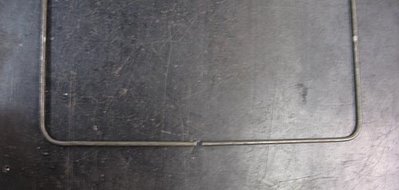

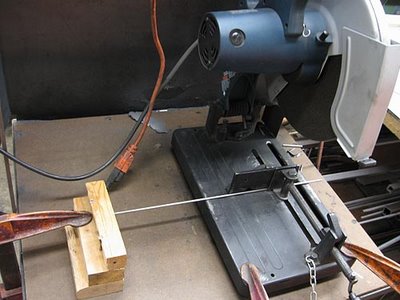

That was it for my shop time on Saturday. I was hoping to get the whole grate welded together, but I will have to finish it next time. After I put these rods on, I will make some handles for it and then move on to the grill body.
Finishing the Grate
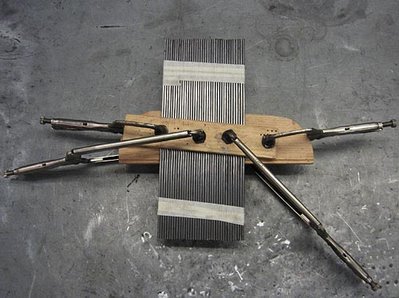
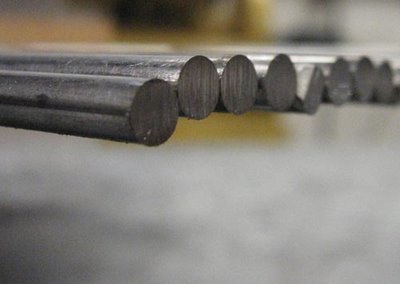
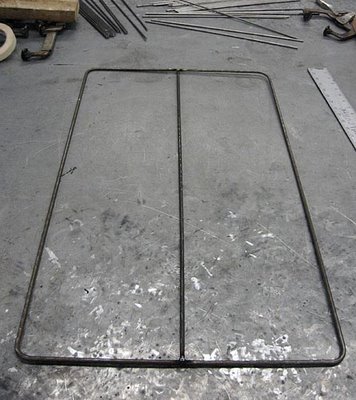

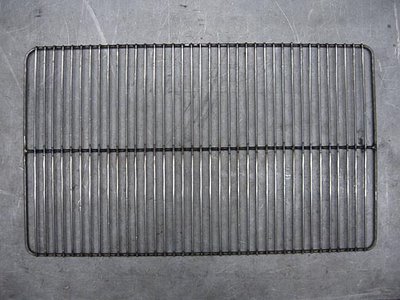

Fabricating the Grill Body





Eventually, I figured out a way to solve this problem: brute force. I jumped up and put all my weight on the corners. It flattened them out a bit and equalized the curve across the sheet.
Fabricating the Grill Body, pt.2







Fabricating the Grill Body, pt. 3






1 Forward, Two Back



It was not to be though. I tacked the lip and everything was gravy. (Tacking means welding a few tiny spots, just enough to hold the pieces in place. Then you go back through and weld the whole seam.) However, after laying down the full weld, I realized the tacks had BROKEN and there was a big ol' gap between the lip and the lid. Once again I underestimated warpage. The weld is too strong now; there is no way for me to break off the lip without destroying the lid itself. I will now have to go back and build ANOTHER lid. *sigh*... It'll take a lot of work to finish this on time. I will attempt to get back to where I was in one day, and then get the hinge built. Next time...
Grindin'






On another note, a bad flu has been sweeping through Evergreen. I caught a mild case, and while it didn't prevent me from doing all this work, my mind is kind of clouded. So I decided not to make a major decision about how to construct the hinge right now. My next work session is on Saturday, and I should be all better by then.
Starting the Frame
- Assemble the frame that will hold everything up from square tubes.
- Attach wheels
- Attach a handle
- Make Flanges inside grill bowl to hold up grates, and flanges on frame to hold up grill bowl
- Make a table that folds out
- Build ash catcher system
- Make a box for charcoal and a cabinet for tools (optional)
- Figure out a functional vent (for smoking)
- Hinge the lid to the bowl.
- Paint everything.
So I was thinking about how to hold up the grate, and I realize that its handles angle out and make it too wide.



After I finished that small tweak, I decide to start constructing the frame. I have reserved a full 20 foot length of 1-1/4" square tube for this purpose.











A productive session, and over the next few days the parts will start coming together. I'm going to be working fast!